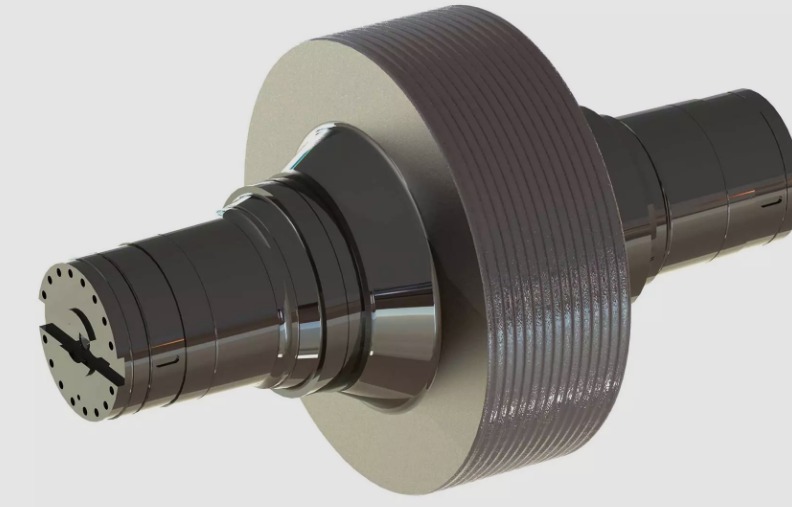
Tribomax® Wear Surface
KEY BENEFIT
- Higher grinding performance
- Lower total cost of ownership
- Flexible hardfacing solution
High-performance, cost-effective grinding with TRIBOMAX® Wear Surface
Tired of your hydraulic roller press wear surface causing breakdowns? The unique TRIBOMAX® Wear Surface from FLSmidth improves grinding performance and reduces the risk of failure. It offers an ideal solution for clinker, slag, and raw mix applications.
Our TRIBOMAX® Wear Solution is a unique, wear-resistant surface for hydraulic roller press installations
It provides significant improvement in roller lifetime and is the most durable wear surface available.
A TRIBOMAX® surface has a built-in roughness and offers a high and constant torque factor due to hard carbide particles embedded in a softer matrix.
A TRIBOMAX surface doesn't need to have patterns, resulting in very limited maintenance. The wear surface has been tested by feeding manganese steel balls into the roller gap without any surface damages appearing.
Optimise the performance of your hydraulic roller press
The TRIBOMAX® Wear Surface was developed specifically to improve the performance of our hydraulic roller presses with a unique wear surface that offers higher grinding performance and lower total cost of ownership when compared to other hardfacing solutions.
Higher grinding performance
Technology based on Plasma Transfer Arc welding offers a highly-controlled metallurgical composition, ensuring TRIBOMAX® yields significantly improved grinding quality and performance.
It’s all about the surface. Special microstructure properties enable TRIBOMAX to provide high surface friction, which eliminates the need for a surface pattern. The TRIBOMAX Wear Surface is also less prone to wear. This avoids the ‘bath tub’ effect, when the areas under greatest pressure, in the middle of roller, exhibit more wear than the edges. In contrast, TRIBOMAX maintains an even surface, enabling a more consistent grinding bed thickness – again improving performance.
Lower total cost of ownership
The quality of the TRIBOMAX Wear Surface improves the availability of the roller press by reducing maintenance needs and the risk of failure.
TRIBOMAX surfaces are guaranteed to offer wear life from 25,000 hours to 40,000 hours, depending on the application. Even in the unlikely event the surface is damaged, it can be repaired in-situ, limiting production downtime. This means that TRIBOMAX has a lower total cost of ownership over the life of the wear surface when compared to traditional hardfacing solutions.
Flexible hardfacing solution
TRIBOMAX is also a flexible solution. A sleeve solution, shrink fitted to the current shaft of the roller press, is the preferred option to reduce the overall cost, but complete rollers with TRIBOMAX surfaces can also be supplied.
The TRIBOMAX Wear Surface can be used in aftermarket applications and can be supplied on any roller size or brands with short lead time.